Studying safely is easier when face masks are part of your basic lab gear
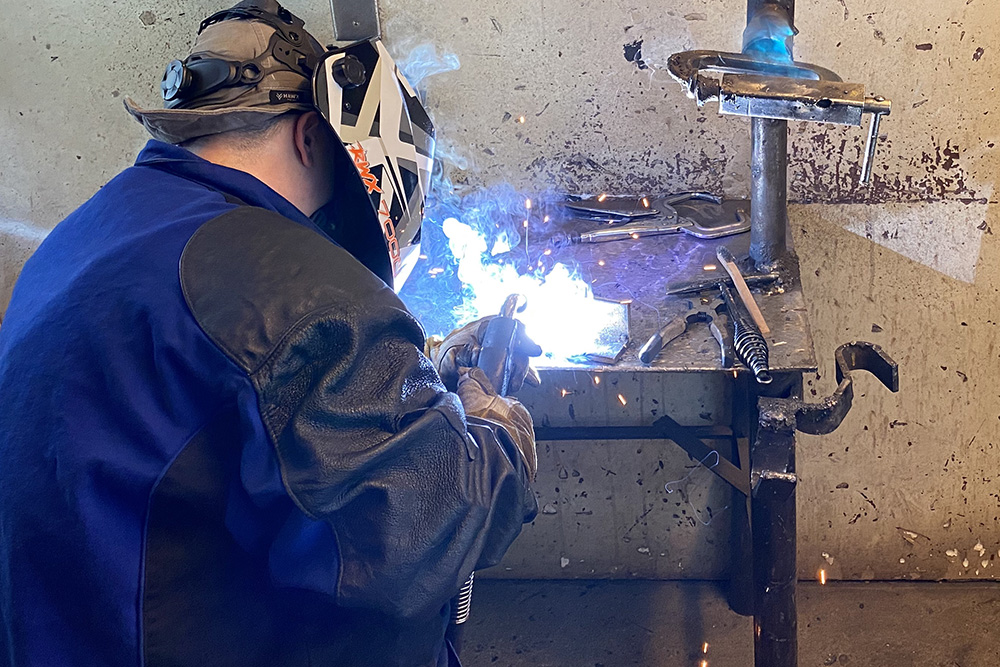
When COVID-19 switched Clark College’s spring quarter classes from on-campus to online learning, Welding Technologies students were ahead of the curve—and therefore were not as affected as other programs with hands-on labs. Instructor John Kuhn already had pivoted to the hybrid model of classes (part online and part in-person) via an online Canvas shell during summer 2019. At the time, it was a good way for students to complete the bookwork portion of their course. During COVID, it has allowed students to not fall too far behind, because they’d already been working online.
“We were pretty fortunate to have gotten started a year before with hybrid,” says Kuhn. “It gave students an opportunity to study more in depth at home. We got a little deeper into theory, the bookwork, utilizing more YouTube welding videos. It proved effectively that they understood the information.”
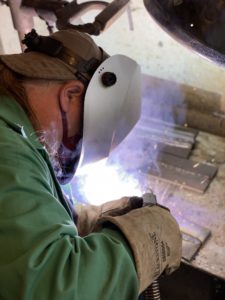
Because safety is paramount, students in the Welding 102 introductory class must pass a welding safety test with 100 percent. In the past, some students had to retake the test in order to pass. Hybrid learning increased students’ understanding of the material and translated into a higher percentage of students who didn’t have to take the test a second time.
Welding students returned to campus labs in mid-June to complete their spring quarter practical welding assignments. Because Welding is a year-round program, the students returned for hands-on welding labs during summer quarter, too.
A program made for social distancing
Even before COVID, welding students already were wearing personal protective equipment and were socially distanced. Students suit up for every lab class: heavy, flame-retardant coat; steel-toed work boots with a metal plate added to protect feet; leather gloves; goggles; and a welding helmet with built-in face shield. Students work in individual welding booths, far removed from other students.
We visited the welding lab as six first-year students were finishing their class project: a flange, a small version of the pressure vessel built by second-year students. Pressure vessels are used to store and transfer liquids and gases under high pressure. Welding on pressure vessels must be exact and meet rigorous standards to withstand working conditions.
All the students we spoke with were eager to enter their chosen field. The outlook is promising: The number of welding jobs in Washington is projected to grow about 3 percent from 2019-2029, about average for all occupations, according to U.S. Bureau of Labor Statistics. In the Vancouver-Portland metro area, the average wage for a welder is $23.98 per hour or $49,887 annually. That’s about $8,000 higher than the median wage nationally.
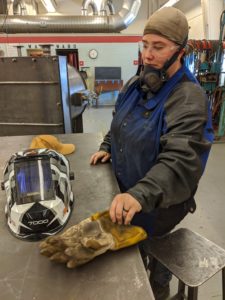
Student story: Jessica Pellham
Jessica Pellham, 26, had no welding experience—and even lacked any experience with tools—when she started the Welding program in fall 2019.
“I kind of started out as a baby,” Pellham laughs. “I wanted to get into a trade. I tried machining. It wasn’t my thing. Then I watched my fiancé’s grandpa welding.”
It intrigued her. She tried welding, and she discovered she had an aptitude for it.
Pellham says, “It’s hard, physical work, but for me, it’s so worth it to do something I love to do.”
“She has excelled fantastically,” says Kuhn.
Pellham works fulltime at a packing warehouse and goes to Clark fulltime, too. When her cohort began, she was one of three women. Now, a year later, she’s the only woman left in her cohort, but there are more women in the second-year cohort.
“I’m hoping to see more women in trades,” she says. “We can do it, too.”
Pellham’s eventual goal is to be hired on a union or government job.
She adds, “I’d love to weld on submarines or ships.”
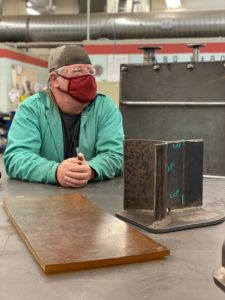
Student Story: Jeff White
At 60, Jeff White of Washougal is the oldest student in the cohort. Two years ago, he was laid off from his job as a boiler operator at Georgia Pacific in Camas, a job he’d held for 30 years. White qualified for the Trade Adjustment Assistance Program, a federal program to retrain displaced workers due to overseas competition. The program has paid for all his college expenses. He is living on unemployment while he attends Clark.
White’s goal is a job in construction welding. He is a fourth-generation Washougal resident, and hopes he does not have to move to find work after he completes the program.
Student story: Ben Barton
Ben Barton, 29, has worked in restaurants since he was 16. A year ago, when he was working as a server at La Bottega in Uptown Village, he was considering making a career change when a co-worker told him about Clark’s welding program.
“I was ready to do something that was stable,” Barton says.
He researched the welding program and applied in summer 2019, but the fall cohort was full. There was so much interest that a second section was opened beginning winter 2020. He started the welding program full-time in January while he continued working at the restaurant 30 hours a week. Then COVID-19 closed restaurants in March, and he was laid off. To make up for the lost income, he applied for unemployment benefits.
“I’m thankful for unemployment,” Barton says. “I’m going to school to further myself so hopefully I’ll never have to be on unemployment again. Financially I’ve been okay. Obviously, you cut back your spending and you end up making your own meals again. Groceries are cheaper than eating out. My girlfriend and I are both in the restaurant industry and are good cooks.”
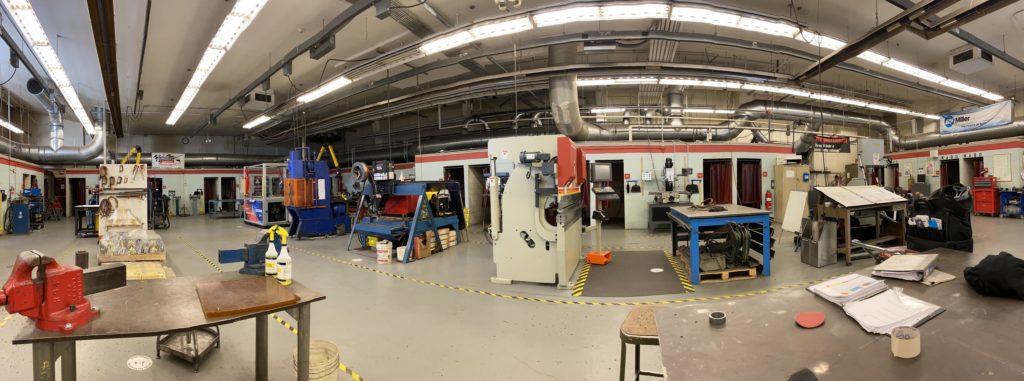
During spring quarter no hands-on labs were offered at Clark. Students kept up with their online bookwork, but they could not get into the labs to practice what they were learning.
“I was really thankful that Clark opened our shop back up for us,” he says. “The welders out there working in the industry are still working during COVID. I was at a stalemate. In limbo. I couldn’t work. I couldn’t do my welding [studies] to further my career.”
“I was one of the few COVID affected positively,” Barton says. “I was juggling school and working. Now I can focus on school.”
Visit www.clark.edu/cc/welding to learn more about the Welding Technologies program.